
Celebrating 10 years of incorporation.
Innovative Construction. Specialist Brick, Block and Stonework.
RENOVATION PROJECTS
#4 Ambleside (SHORT Version)

During - Large structural steelworks
"Ambleside", a property located within a quiet little village, in Nottinghamshire. The new owners had their vision, foreseeing that the building had great potential. So, they purchased their new home with their ideas kept safe in mind for the future.
Several years later, after the funds had been raised, the professionals were called in..
The architects designed, the engineers calculated, and we, the Heritage Probuild Team, we delivered.
This was a very challenging project from the get go. Probably about, as complicated as you can get, when modifying a domestic building structurally. Many people would have suggested to simply demolish and rebuild it from scratch, but this would have been a far more expensive alternative, and I knew we could deliver, so we did.
​
Tasks involved: removing an entire chimney stack from top to bottom, excavating inspection pits to confirm the foundation structure of the building. Removing: existing supporting steelwork, structural timbers, beams, and load bearing masonry walls, sliding doors, existing plumbing and electrics. Basically, we stripped everything out to bare structure and then made large holes in the external walls. At this point, the working areas of the house were very vulnerable to collapse. Thankfully, our knowledge, expertise, and competence, enabled us to safely prevent this from occurring, and we could confidently begin to rebuild the house to its new design specification.
​
Comprised of more than 20 new steel pieces, to become the new structural components, which were specially manufactured with an intended purpose. It was our mission to install them into place, before rebuilding the walls and floors around the new framework. Thus, creating: the new, minimalistic, modern, and seamless, open plan living space, complete with a new loft conversion and bedroom. All whilst 'levitating' a huge chunk of the existing building overhead, whilst we assembled underneath. Very risky work indeed. Yet, no accidents, no near-misses, no errors, and no problem for the Probuild team.
​
Please watch the videos above and below to see how we carried out our objectives.​​
#4 Ambleside (LONG Version)
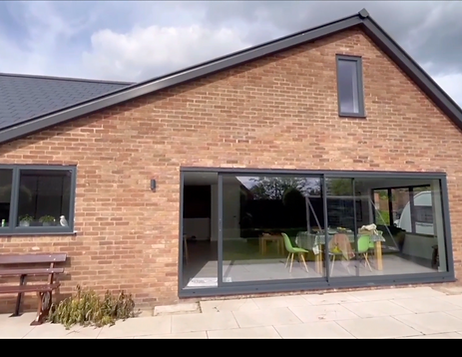
After - Rear elevation completed
RENOVATION PROJECTS
#3 Masonry Restoration

Before - Cement rendered walls
They say that fashion trends in cycles, fades out, and then eventually comes back into style..
Once upon a time, it would have been something special, very uncommon and unaffordable (for most people) to go to the trouble to render plaster over a stone built house of this size, or any house at all, in fact. A hundred years ago or more, somebody rather wealthy and fashionable did exactly that to this property. For decades after, this building would have gleamed both, bold and bright, looking very beautiful against the blue sky and green landscape where it is located, near St Austell in Cornwall. And, it would have been very noticeable indeed.
​
Today, however, we see render everywhere. Yes, pretty, but much more common, therefore, less impressive. The reason being, is that modern construction methods and materials have changed over the years with the goal of creating buildings which are better insulated, quicker to build, and damp resistant. One of the main building materials which we now commonly use to erect our cavity wall masonry structures here in the UK, is the 'concrete block'.
We build with concrete blocks where possible, because of the reduced amount of time required in man hours, to erect these masonry walls, when compared to building with bricks and / or stone. Which, in turn, equates to cheaper labour costs. Concrete blocks are also cheaper to manufacture than bricks and stone. The downside of building with blocks, is that, compared with bricks and stone, a block wall is rather unsightly hence, 'the rendered block wall finish' which is far prettier. Some blocks can also be quite porous and so, a coat of render is often required to 'waterproof' the external side of the block wall and prevent moisture ingress into the building.
Modern 'through colour' renders are beautiful in their own right. They have many qualities and are a far superior product when compared to the traditional cement and lime renders of the past. Some of the benefits are that, there is no need for painting as they come pre-coloured in a variety of colours as standard, they are breathable, which helps with lowering humidity levels inside and therefore, limiting the internal mould growth throughout the inside of the building. They are relatively easy to apply which helps reduce labour costs and they only require a good pressure wash as maintenance, once every couple of years - which will keep the walls looking fresh! ​​
​
Now, back to stonework and the present day.. Ironically, to have a wall built from natural stone is a very expensive process indeed. By far in fact, the most expensive way to build a modern house. From the initial mining of the stone, to the cutting and shaping of it into smaller, usable pieces. The 'dressing' of the stones to make them fit the modern house deign (cavity wall structure), to the manual handling, sizing, grading, laying and traditional (flush) jointing of the stonework. These are all elements which contribute to increased man hours and higher build costs. A hundred years ago or more when we were building stone houses as 'solid wall structures' there was far less cutting and shaping of the stones to be done. Simply because there was no cavity, and no insulation built into the fabric of the walls. Even though more stones were used to build the houses, the process still would have been less timely, due to the fact that the houses were less complicated to build. All of these extra costs far outweigh that of brickwork and block work structures, with rendered finishes. Which, in turn result in fewer natural stone houses being built, making them more desirable and prestigious to own, due to their rarity.
​
Whilst working on our renovation project down in St Austell, it was requested by our clients to "repair and restore the external face of the building". We gave them their basic options but concluded that without further investigation into the condition of the structure underneath the cement render, that we couldn't yet advise them to the best of our knowledge. We agreed to carefully remove a discreet patch of the contaminated plaster to discover a beautiful, cream coloured, granite stone construction, which lay hidden below for all of those years. Our clients and I were delighted with the discovery and in this moment they excitedly asked us to continue to remove all of the existing render, repair and restore the stonework and bring this building back to its original glory. I replied "Yes, of course! Let's add some more period features along the way and make this building something special".
​
The finished product turned out to be something special indeed.
​
Restoration Work Included:
​
-
Removal of cement render which surrounded the entire building
-
Raking out all mortar joints of the stonework in preparation for lime pointing
-
Lime mortar repointing all of the newly exposed stonework
-
Removing and rebuilding areas of damaged stonework throughout
-
Installation of reclaimed granite stone, stooled, window sills
-
Removal and replacement of brick window and door surrounds with a better quality, reclaimed cream brick
-
Installation of real oak lintels to form the new window and door heads
-
Dismantle and rebuilding of two chimney stacks using the original bricks
-
Replace the roof covering using the original 'Delabole' slates and reclaimed ridge tiles
-
New uPVC sash windows
-
Reclaimed hardwood front door.
RENOVATION PROJECTS
#2 Victorian Detached - Part 1

After - post renovation progress
Displayed above is a beautiful Victorian stone building which was in need of some modern upgrades. This property is located near St Austell in Cornwall.
​
Sadly, for most of the work carried out here we didn't record much of the progress due to technical issues with the action cameras. This is very disappointing for us because some of the work which we have produced has been both rare and spectacular.
​
However, we do have photographs displayed in our gallery section should you be interested in some of the transformations.
​
There is still much work left to do on this property as its requiring a full house renovation which will take some time. This is due to the expense of the work involved and with it being located so far away. It is however a project which we are hoping to see through to the end and we expect to see it completed over the next five years.
​
The first video displayed above as "part one" of a potential series is of a majority renovation of the living room, with the remaining finishing touches yet to be carried out.
​
Tasks involved and completed as of present day:​​
​
-
removal of lime plaster from the walls and ceiling
-
breaking out and removal of decayed concrete floor
-
chopping out mortar joints and repointing the stone work to create a feature wall
-
expanding the existing fireplace making larger and installing a steel lintel over the opening
-
damp proofing membrane and PIR sub floor insulation board
-
underfloor heating pipework installation (warm water system)
-
dry mix floor screeding (mixed on site)
-
large granite stone fireplace and slate hearth installation
-
extensions of both lighting and power circuits
-
sound proofing
-
plaster board installation, final prep work and plastering
RENOVATION PROJECTS
#1 Victorian Semi Detached - Part 1
Part 2
Working on a renovation project at Thorpe Road, Melton Mowbray. Our objective was to reveal and create the open plan style kitchen and living space, which was hidden and separated between three load bearing walls.
​
Tasks involved:
-
temporarily supporting the building with acro props and scaffold boards
-
removal of three load bearing brick partition walls
-
installation of three steel beams​ on padstones and brickwork over between floor joists making solid
-
installation of concrete lintels over window and door openings
-
supporting unused chimney stack (where now removed from the ground floor) to create space
-
excavation and spoil removal of the existing floors and substrate
-
creating a large opening in an external wall for a bi-fold door
-
building of a nib wall to make an equal sized bearing for a new steel beam over structural opening
-
toothing in and bricking up of coal shed doorway
-
solid floor construction of hardcore, membrane and concrete
Part 3
Part 4
Continuing through parts three and four of this project.
​
Tasks involved:​
​
-
installation of PIR board sub floor insulation
-
electricians first fix wiring
-
underfloor heating (warm water system)
-
dry mix floor screeding (mixed off site)
-
removal and replacement of damaged brickwork underneath rear window
-
installation of a new steel lintel over window opening and bricking over between temporary acro supports
-
stud partition walls erected with sound proofing insulation creating en suite bathroom and downstairs toilet
-
building a new and improved design front boundary wall
-
careful removal and rebuilding of a large four pot chimney stack
-
grinding out and repointing the entire brickwork face with a yellow sand, white cement and lime mix.